The extension of the project timeline brought enhanced significance to this year’s annual meeting, which emphasized strategic planning and logistical fine-tuning. With the project set to conclude by the end of June 2024, we dedicated our efforts to ensure that every session and activity throughout the meeting was geared towards aligning with our extended objectives.
Here’s a brief overview of the primary events and discussions from each day:
- Day 1 Recap (6th Nov): We delved into use case progress, exploring hub-to-hub collaborations, port, airport, and forklift innovations, and reflected on our journey thus far. The day concluded with an in-depth review of our work packages and a dynamic wrap-up discussion.
- Day 2 (7th Nov): Today we are at📍FH OÖ Campus Steyr | Fakultät für Wirtschaft und Management! The agenda is all about strategic vision: our Project General Assembly session is set to review objectives and facilitate pivotal decisions through voting. Post-lunch, we’re off to 📍DigiTrans GmbH test centre for automated driving for a hands-on demonstration that’s bound to inspire.
- Day 3 (8th Nov): Get ready for a fusion of fun and foresight with our LEGO series play workshop. Creativity at its peak: constructing the very future of Autonomous Vehicles with innovation as we pave the way for Autonomous Vehicles, one LEGO block at a time!
DAY 1 - Nov. 6th: The Latest Advancements in Port, Forklift, Airport and Hub-to-Hub Operations
The ongoing development of the EZTug, an automated tug vehicle designed to optimize PORT logistics, is advancing through a three-phased approach to enhance trailer transfer efficiency: Phase I handles trailer moves within the terminal; Phase II covers the last-mile delivery including gate processing, and Phase III expected to conclude in early October 2023, involves ship loading and unloading. Key achievements include a completed demonstration phase and integration with a Fleet Management System (FMS). Future milestones include delivering the “Report on Automated Port Logistics Operations” by the end of November and finalizing “Testing Methodology and Evaluation” with a focus on safety. Operational boundaries are set for EZTug, which excludes reversing and trailer connections and include a human presence in the vehicle for safety at this stage of the technology’s development. This strategy underscores the meticulous planning in adopting automation in ports, prioritizing efficiency, and safety.
The FORKLIFT use case demonstrates a comprehensive integration of advanced sensor technologies and hardware modifications to improve safety and efficiency in operational environments. Incorporating a real-time obstacle detection system, the forklifts are equipped with the AWARD sensor setup that captures the surroundings and alerts them to imminent risks. ADS (Autonomous Driving System) development has resulted in an intelligent machine capable of decision-making and problem-solving in dynamic settings. Enhanced pallet detection algorithms ensure precise manoeuvring, while fleet management systems monitor and analyze the forklift’s performance data for continual improvement. This integration signifies a significant leap in industrial automation, emphasizing safety, precision, and data-driven management for logistics operations. This use case consists of three use cases: Phase I: Safe movement in open environments; Phase II: Autonomous loading of a single hand-picked pallet to a defined location; and Phase III: Complete automated loading and unloading of a full truck.
The KAMAG AV HUB-to-HUB use case is progressing through its phases: After major restrictions to public traffic in Phase I the operation was continuously optimized until in Phase II operation in normal traffic with only minor restrictions was possible. The improvements included the adapted regulation of the intelligent traffic light connected to the automated vehicle via C-ITS communication to reduce congestion. Currently, the focus is on finalizing the operations and testing the vehicle with teleoperation in a controlled environment. There is a continuous need for thorough testing and data analysis to evaluate autonomous operation and teleoperation under various weather conditions and to refine safety measures and emergency protocols, particularly concerning the transport of loaded goods and compliance with traffic regulations.
In the AIRPORT use case, the EZTow autonomous vehicle is making strides in operational testing and integration. Achievements include successful sensor tests under environmental conditions, completion of Taxi Lane Departure (TLD) tests and ongoing winter tire grip assessments. The next steps involve additional sensor testing in snowy conditions, restarting data collection, and progressing to manual and automated phases of operation. A noteworthy point for future coordination is the sharing of data between work packages to streamline efforts. The EZTow’s route for luggage and cargo handling includes predefined start and end points within the airport, with a designated waiting area, optimizing the flow of ground operations and enhancing efficiency in airport logistics.
The next steps for our airport use case involve additional sensor testing in snowy conditions, restarting data collection, and progressing to manual and automated phases of operation.
DAY 2 - Nov. 7th: the PGA Meeting & the Hub-to-Hub Spotlight
The Project General Assembly (PGA) Meeting
The Project General Assembly (PGA) Meeting was hosted at the FHO premises in Steyr, where the esteemed Professor Wolfgang Schildorfer, Vice-dean for Research in Transport Logistics and Mobility at the University of Applied Sciences Upper Austria – Steyr Campus, extended a warm welcome to the consortium members.
This pivotal assembly serves as a strategic gathering for EU-funded project partners to synchronize their efforts, assess the project’s trajectory, and collaboratively navigate the complexities of project management in accordance with EU directives. It functions as a crucial forum for deliberation and decision-making, ensuring that the project adheres to its outlined goals while fostering a cohesive and transparent partnership among the diverse organizations involved.
Spotlight on the Hub-to-Hub use case!
The test centre for automated driving at DigiTrans GmbH stands out for its exceptional facilities, which are meticulously crafted to mirror real-world operational scenarios with impressive realism and attention to detail. The team has done an exemplary job in creating a testing environment that not only meets but surpasses the expectations for a state-of-the-art development site, ensuring that simulations conducted here offer high fidelity insights into actual performance and conditions.
The Digitrans Test Center for Automated Driving in Austria offers an excellent opportunity to replicate complex traffic scenarios for automated passenger cars as well as commercial vehicles on a modern test site for automated and connected vehicles. Thanks to Europe's most modern Outdoor Rain Facility and a great amount of expert knowledge, the Digitrans team can carry out extensive tests under adverse weather conditions to achieve a more stable and a safer operation of automated vehicles in real-life operation.
At the DigiTrans GmbH test centre for automated driving in📍Saint-Valentin, Austria, we were front and centre for the dynamic conclusion of the TII KAMAG Autonomous Vehicle (AV) Hub-to-Hub operation, marking the testing of its final phase. The demonstration was groundbreaking, featuring the autonomous mode and teleoperation with a safety driver providing an additional layer of oversight.
🥁 The audience was treated to a live showcase, replete with complex scenarios that mirror the intricacies of actual use cases – managing crossways, engaging with gate systems, and executing precision turns.
💡 Here, the safety driver is sitting in the office and takes over the control of the automated e-truck via remote maintenance. This climactic phase draws from the successes and learnings of earlier stages, with a pronounced focus on eliminating the dependency on safety drivers. The strategic shift to DigiTrans GmbH‘s controlled environment for teleoperation trials allowed for comprehensive data gathering under a spectrum of weather scenarios, significantly reinforcing safety measures. This was a calculated step to rigorously put to test and solidify the AV system’s operational readiness and dependability.
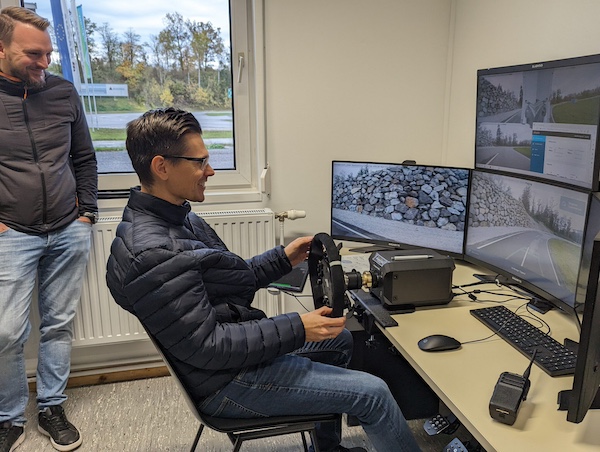
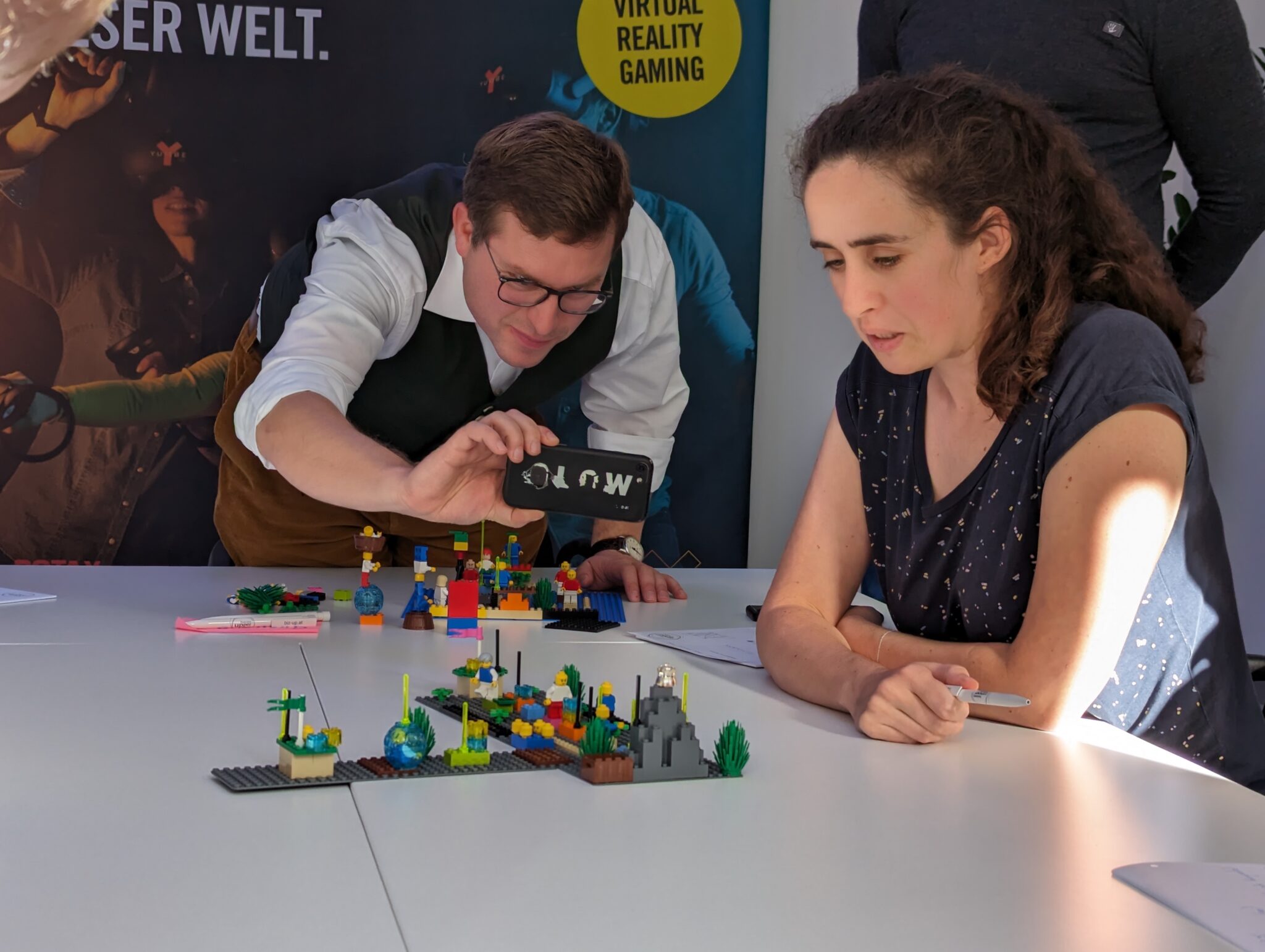
DAY 3 - Nov. 8th: The LEGO Serious Play
We shifted gears into a realm of imagination and strategy with our LEGO series play workshop. The hands-on session was a sandbox of innovation, where the building blocks of tomorrow’s Autonomous Vehicles took shape, guided by the imaginative insights of today’s pioneers.
Building Blocks of Innovation! Linz buzzed with creativity during our LEGO workshop, a vibrant session symbolizing the endless possibilities in the world of Autonomous Vehicles. Business Model Workshop: each LEGO block not only sparked imagination but also represented the future of transportation, one innovative piece at a time. This engaging workshop showcased the essence of the AWARD-H2020 project: a fusion of diverse ideas and expertise, all coming together to shape a visionary path for transportation technology.
Originally posted on: AWARD-h2020